Waterproof performance of marine wiring harness
- 2025-04-07 16:57:02
- by Admin
Material and protective layer design
Selection of Waterproof Materials
- The outer layer of the wiring harness is coated with waterproof rubber, silicone or flame-retardant plastic to prevent moisture penetration and slow down aging.
- Key connection points (such as terminals) need to use galvanized or nickel plated metal to enhance corrosion resistance.
Sealing materials and processes
- Using TJD-103J waterproof sealing tape, its self-adhesive and shape following properties can adapt to cable bending and vibration, and the sealing effect is long-lasting.
- The connector uses silicone sealing rings or potting glue to ensure that there are no gaps at the interface.
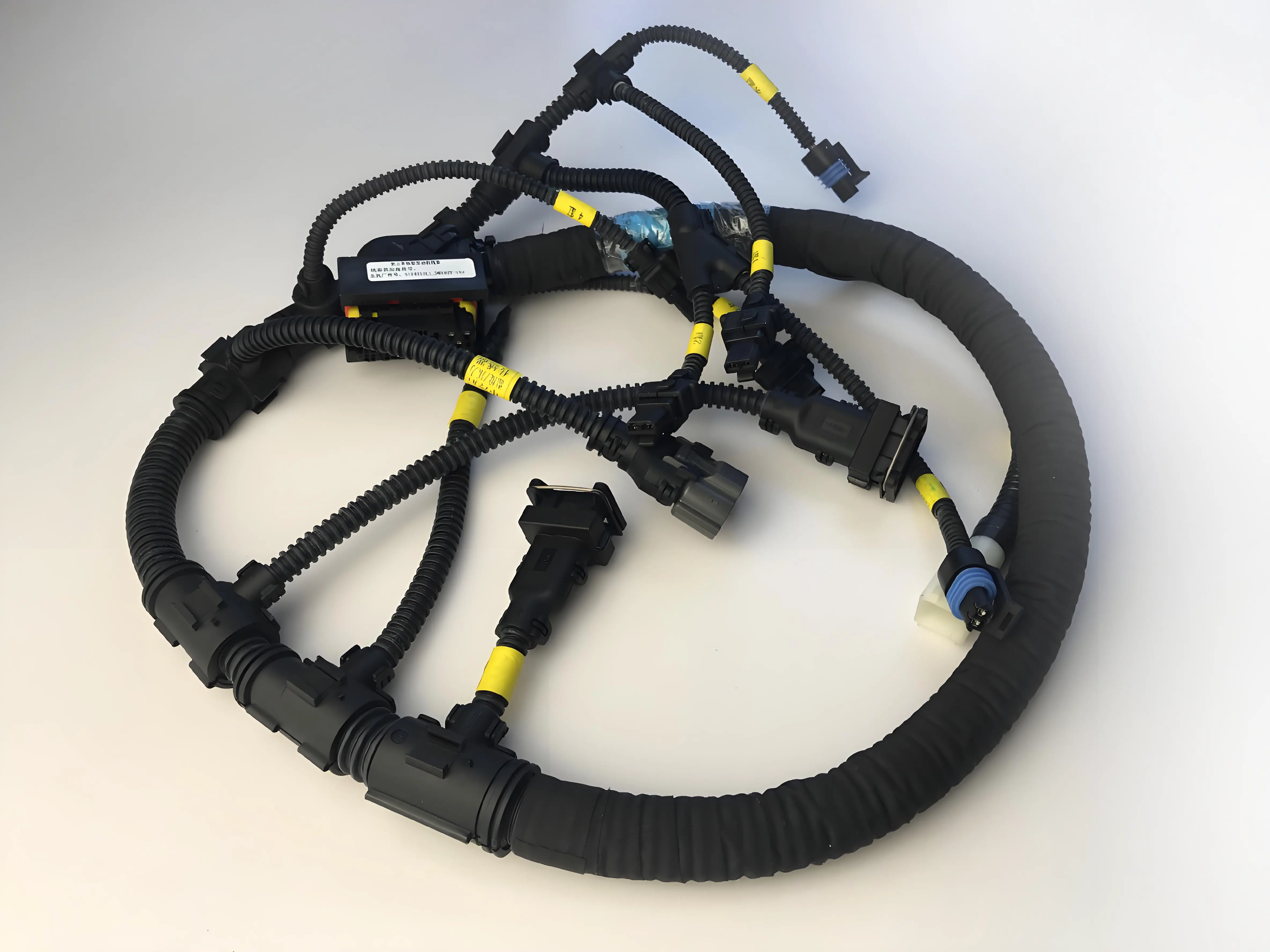
Structure and Process Control
Connector and Terminal Protection
- Select IP67/IP68 protection level connectors and verify the sealing through air tightness testing (pressure 20kPa, holding for 5 seconds).
- Special molds are used for terminal crimping to ensure that there are no burrs or damages after crimping, and to prevent moisture from entering the wire core.
Reinforcement of outer layer of wire harness
- Wrap solder joints or wiring points with heat shrink tubing to prevent copper wires from being exposed and causing oxidation or short circuits.
- The wire harness sheath is made of HDPE or PVC material, which has both wear resistance and mechanical strength, and is suitable for high humidity environments in ship cabins.
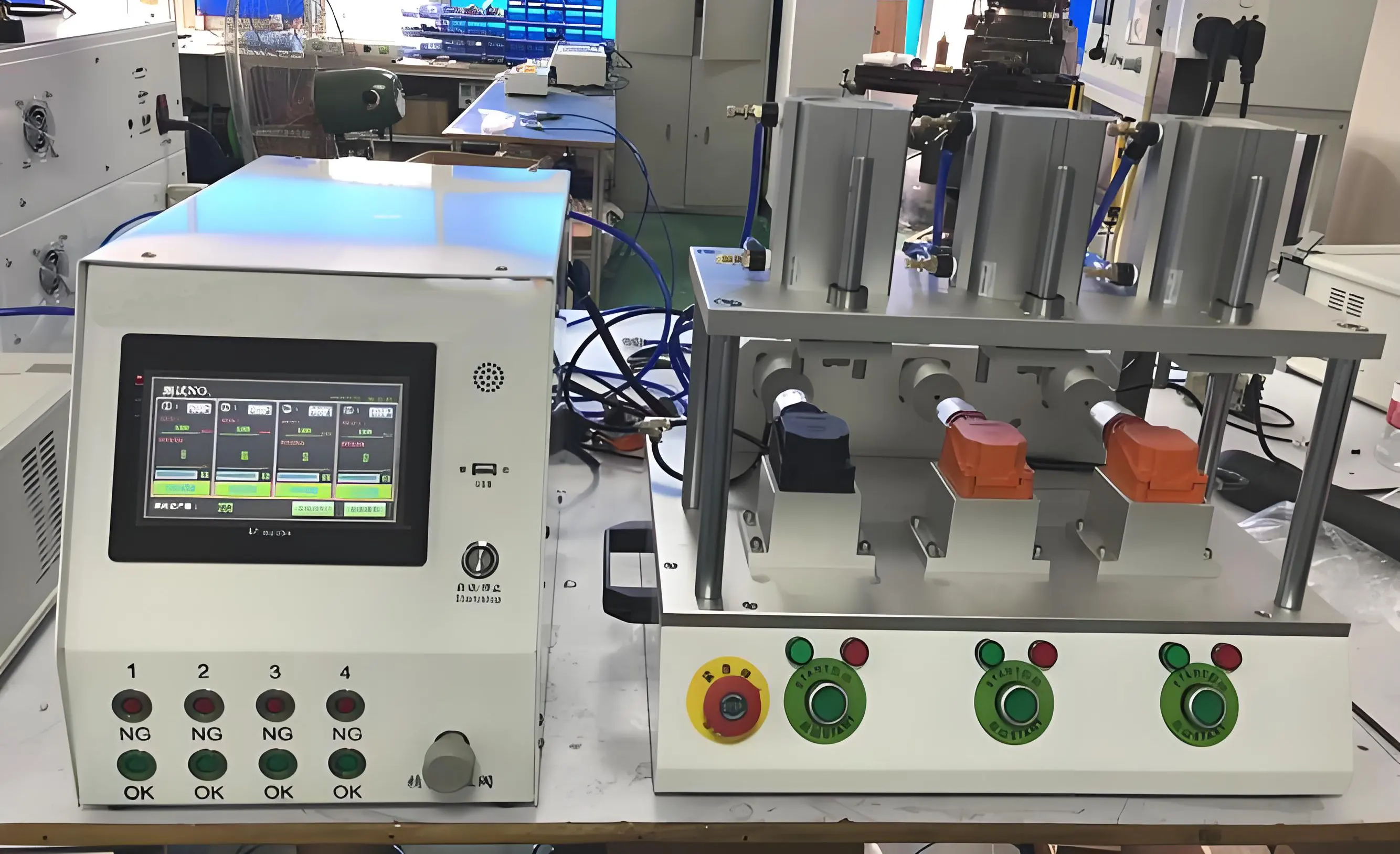
Environmental adaptability verification
Salt spray and temperature and humidity cycling test
- Simulate a high salt spray environment in the ocean for a 48 hour salt spray test to detect corrosion of wire harness metal components.
- Test the aging rate and sealing stability of the sheath material under high temperature and high humidity cycles (such as 85 ℃/85% humidity).
Mechanical vibration and wear resistance testing
- Simulate the bumpy environment of a ship on a vibration table and check whether the wire harness sheath is cracked or the terminals are loose.
- Friction test verifies the wear resistance of the sheath to prevent long-term wear from causing the waterproof layer to fail.
Waterproof testing of marine wiring harness
Testing method |
Test conditions |
Judgment criteria |
Applicable scenarios |
Static immersion test |
The wire harness is vertically or horizontally immersed in an environment with a water depth of 6m and a water temperature of 20-40 ℃ for more than 30 minutes, followed by a 30 minute treatment with a constant temperature and humidity of ≥ 85%. |
There is no water leakage inside, and the electrical performance is normal |
Overall waterproof performance verification |
Dynamic water pressure test |
Simulate wave impact using water pressure method (2.5-20kPa water pressure) or bed load method (mechanical load applied after immersion). |
No sheath damage or interface leakage |
Assessment of resistance to water pressure impact |
Airtightness testing |
Inflate with an air tightness tester to 100kPa, stabilize for 5 seconds, with a maximum leakage limit of ≤ 50Pa, or perform non-destructive testing on compressed air. |
IP67/IP68 protection level meets the standard |
Verification of connectors and sealing points |
Salt spray and temperature and humidity cycling |
48 hour salt spray test (simulating high salinity marine environment) and high temperature and high humidity cycle (85 ℃/85% humidity). |
Metal parts have no corrosion, and the protective sheath has no aging or cracking |
Corrosion resistance and sealing stability of materials |
Note:
- IP rating: The second digit represents the waterproof rating (e.g. IP67: short-term immersion; IP68: continuous immersion).
- Priority determination: Airtightness testing (rapid qualitative) and immersion testing (quantitative verification) need to be used in combination.
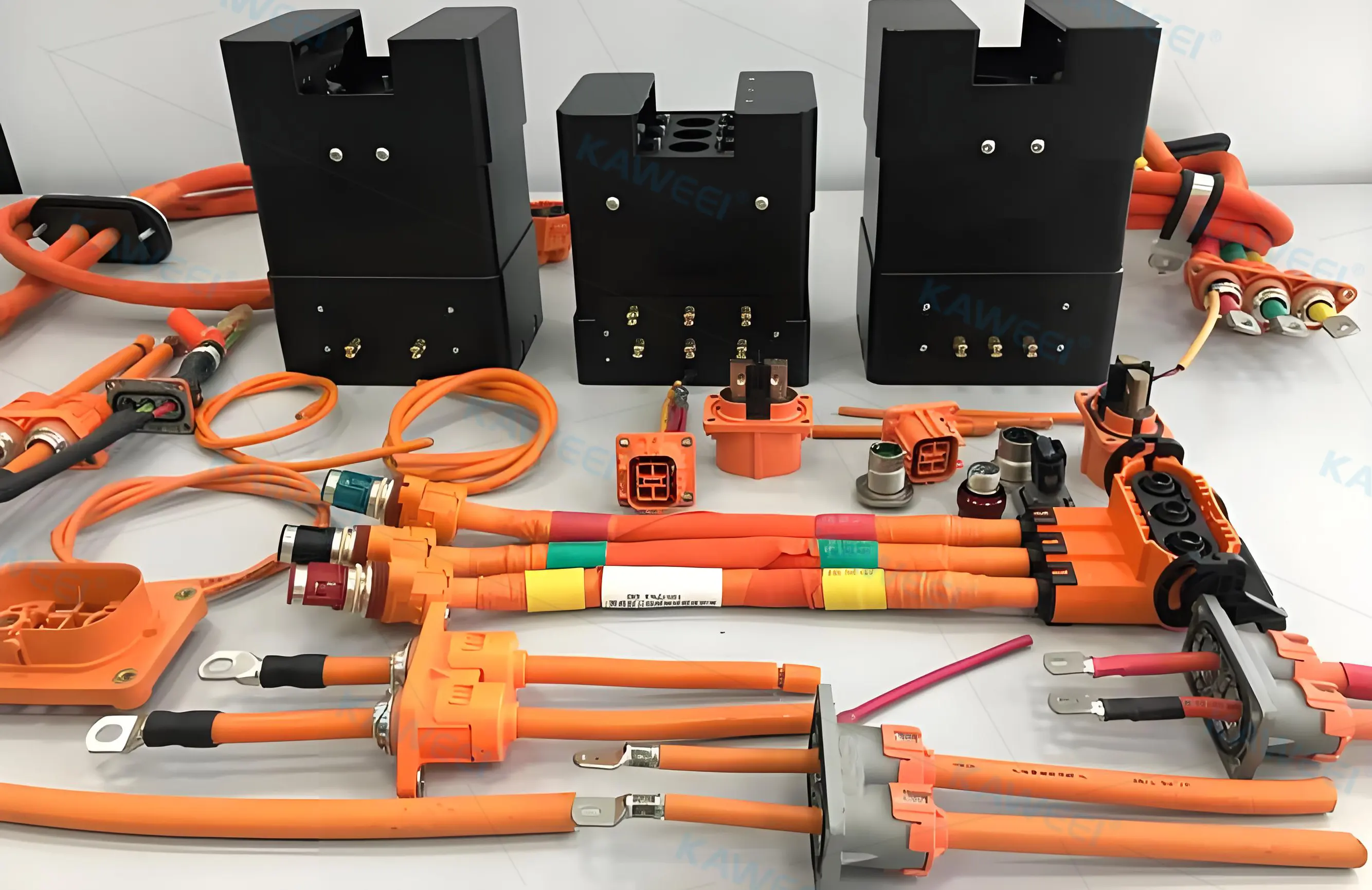
The waterproof performance testing of marine wiring harnesses needs to be combined with standard immersion testing, air tightness verification, environmental simulation, and process inspection to ensure their reliability in high humidity, high salt spray, and mechanical vibration environments in the ocean. Core indicators include IP67/IP68 protection level, leakage pressure threshold (≤ 50Pa), and material durability.