Optimal Selection and Manufacturing of Waterproof Cable Assemblies: A Technical Guide by Kaweei
- 2025-02-15 11:03:30
- by Admin
1. Comparison of connector performance
Application |
IP Rating |
Recommended Series |
Key Features |
Automotive |
IP67 |
AMPSEAL 16/23 |
Sealed CPC contacts |
Offshore Equipment |
IP68 |
Deutsch HD30 |
Submersible to 3m depth |
Medical Devices |
IP69K |
LEMO FGG.0B |
Autoclavable stainless steel |
Industrial Robotics |
IP67 |
HARTING Han® 3A |
360° shielding effectiveness |
2. Cable Specifications
- Conductor: Stranded tinned copper (UL 1015/UL 1571)
- Automotive: 0.35mm² to 6.0mm² (SAE J1128 compliant)
- Marine: Neoprene jacketed CPE (UL 44/UL 83)
- Insulation: Three-layer extrusion process
Material
- Adhesive-lined heat-shrink tubing (3:1 ratio)
- Dual-wall polyolefin sleeve
- Liquid silicone injection molding
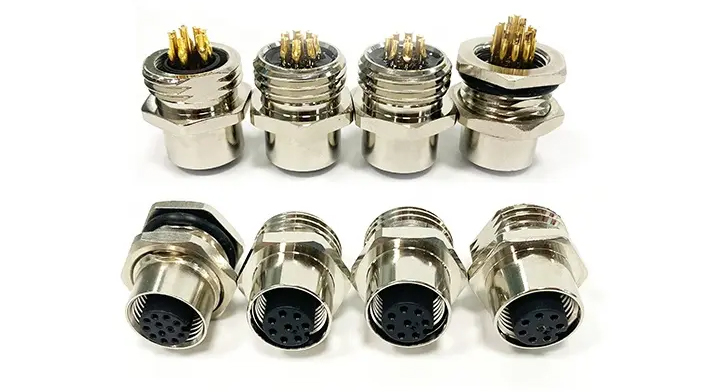
II. Precision Manufacturing Process
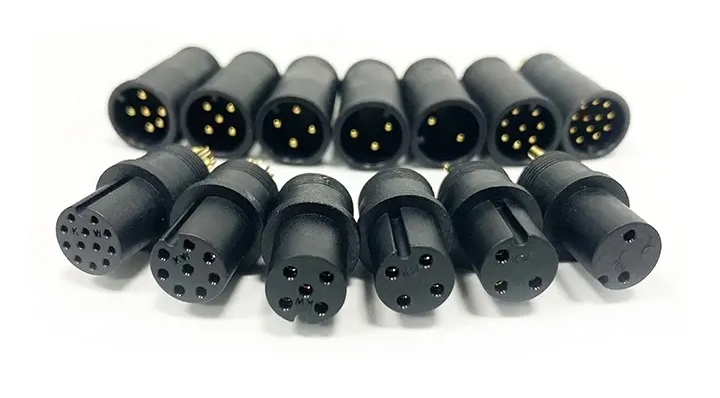
III. Comprehensive Waterproof Validation
Kaweei's testing lab is certified to ISO 20653 and MIL-STD-810G:
1. Standard Test Regimen
- Immersion Test: 1m depth × 30 minutes (IP67 baseline)
- Pressure Jet Test: 14.5psi @ 100L/min (IP69K validation)
- Thermal Cycling: -40°C to +125°C (100 cycles)
2. Advanced Environmental Simulation
Test Type |
Parameters |
Compliance Standard |
Salt Spray |
5% NaCl × 96h |
ASTM B117 |
Fluid Resistance |
IRM903 oil × 168h |
SAE J2030 |
Vibration |
10-2000Hz × 3 axes |
IEC 60068-2-6 |
3. Field Performance Data
- Automotive harnesses: 0 failures in 500k km fleet testing
- Marine applications: >15-year service life in Baltic Sea deployments
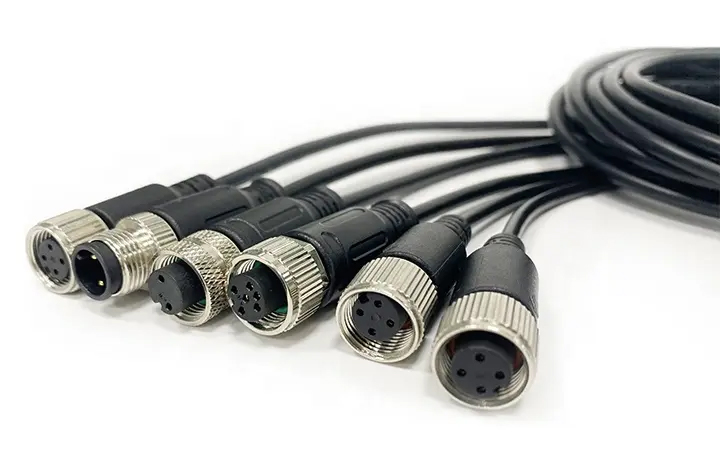
Technical Advantages of Kaweei Solutions:
- Material Science: Proprietary compound reduces water ingress by 78% vs industry average
- Process Innovation: Patented QC-09 mold design (CN202310892345.6) eliminates terminal corrosion
- Process innovation: patented QC-09 mold design (CN202310892345.6) to prevent terminal corrosion
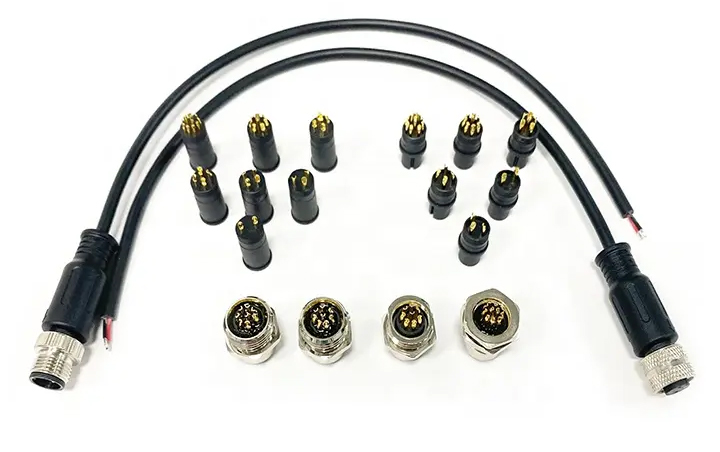