How to crimp terminals?
- 2025-03-10 11:55:19
- by Admin
As the core component of the wiring harness, terminals ensure the stability and reliability of electrical connections, directly affecting the functionality and safety of the entire system.
Crimping terminals are an important process in wire harness manufacturing, used to ensure the reliability of electrical connections and the mechanical robustness of core steps, directly determining the stability of signal and power transmission, and avoiding equipment failures or safety hazards caused by poor contact.
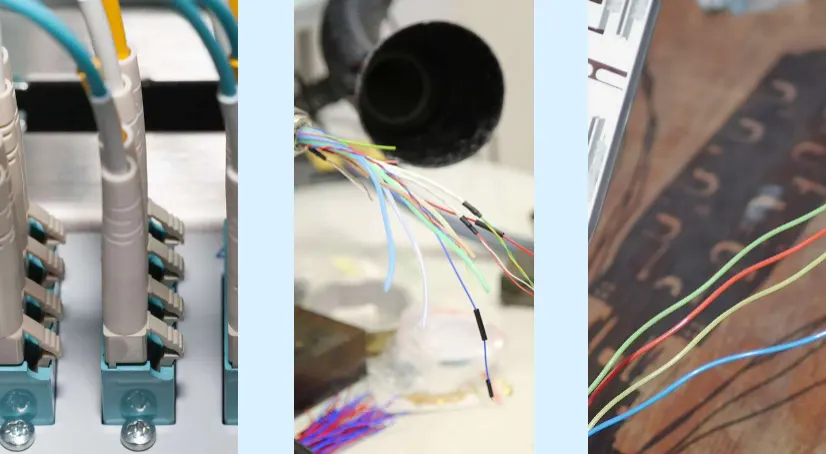
So you know how to crimp terminals of high quality?
I. Terminal crimping basic concepts and principles
Terminal crimping definition and role
- Definition: Terminal crimping is a kind of technology that connects wires and terminals through pressure, which is a commonly used connection method in electronic engineering.
- Role: to realize the electrical connection and mechanical connection, to ensure the reliable transmission of current between the wire and the terminal.
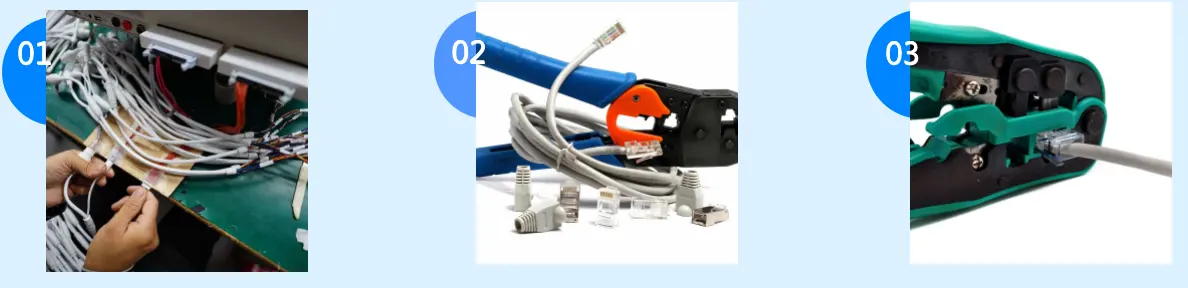
II. Crimping principle and process
- Crimping principle: the use of crimping tools squeeze pressure, so that the terminals and wires between the plastic deformation of the metal, the formation of close mechanical and electrical connections.
- Preparation tools and materials: Select the appropriate crimping tools and terminals and prepare the wire to be crimped.
- Stripping: According to the terminal requirements, strip the wire insulation to a certain length, exposing the internal metal core.
- Cleaning treatment: Clean the contact surfaces of wires and terminals to remove oxides and impurities.
- Placement of terminals: Place the terminals in the corresponding position of the crimping tool to ensure the correct orientation of the terminals.
- Crimping operation: Place the wire into the terminal and start the crimping tool for the crimping operation.
- Check the quality of crimping: check whether the crimped terminal is firm, has good conductivity, and has no loose, broken, and other phenomena.
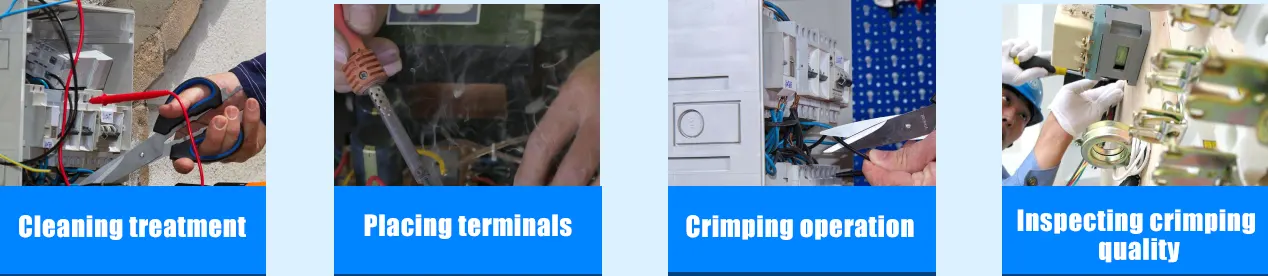
III. Common crimping problems and solutions
- Poor crimping: manifested as high contact resistance, easy to loosen or fall off. Solutions include checking whether the crimping tool and terminal match, adjusting crimping parameters, and ensuring that the wire and terminal are clean.
- Wire damage: In the crimping process, the wire may be over-squeezed or scratched. Solutions include choosing the right crimping tool and parameters, ensuring that the wire is placed correctly, and avoiding over-squeezing.
- Terminal deformation or damage: improper operation or tooling problems lead to terminal deformation or damage. Solutions include checking and replacing damaged terminals, adjusting crimping tool parameters, and ensuring proper operation.
- Looseness after crimping: After crimping is completed, there is looseness between the terminals and wires. Solutions include re-crimping, adding locking measures such as spot welding or using locking agents.
Kaweei is a manufacturer specializing in the wire harness industry. With years of experience in high-precision terminal crimping technology, Kaweei ensures that each connection point has consistent metal bite strength and conductivity, eliminating virtual connections and disconnections at the root and maintaining stable transmission performance of the wire harness under extreme working conditions.
Next, I will introduce to you the IPC620 standard