High temperature resistant 125 ℃ wire harness sheath
- 2025-04-06 14:34:27
- by Admin
The high-temperature resistant 125 ℃ wire harness sheath material is a cable outer protective material designed specifically for high-temperature environments. It can maintain physical stability of the wire harness under long-term exposure to 125 ℃ working conditions, while meeting requirements for electrical insulation, mechanical protection, and chemical resistance.
Material definition and technical characteristics
Basic Definition
The high-temperature resistant 125 ℃ wire harness sheath material refers to the sheath layer developed through polymer modification or composite technology, which can continuously work at a temperature of 125 ℃ and have a short-term temperature resistance of over 150 ℃.
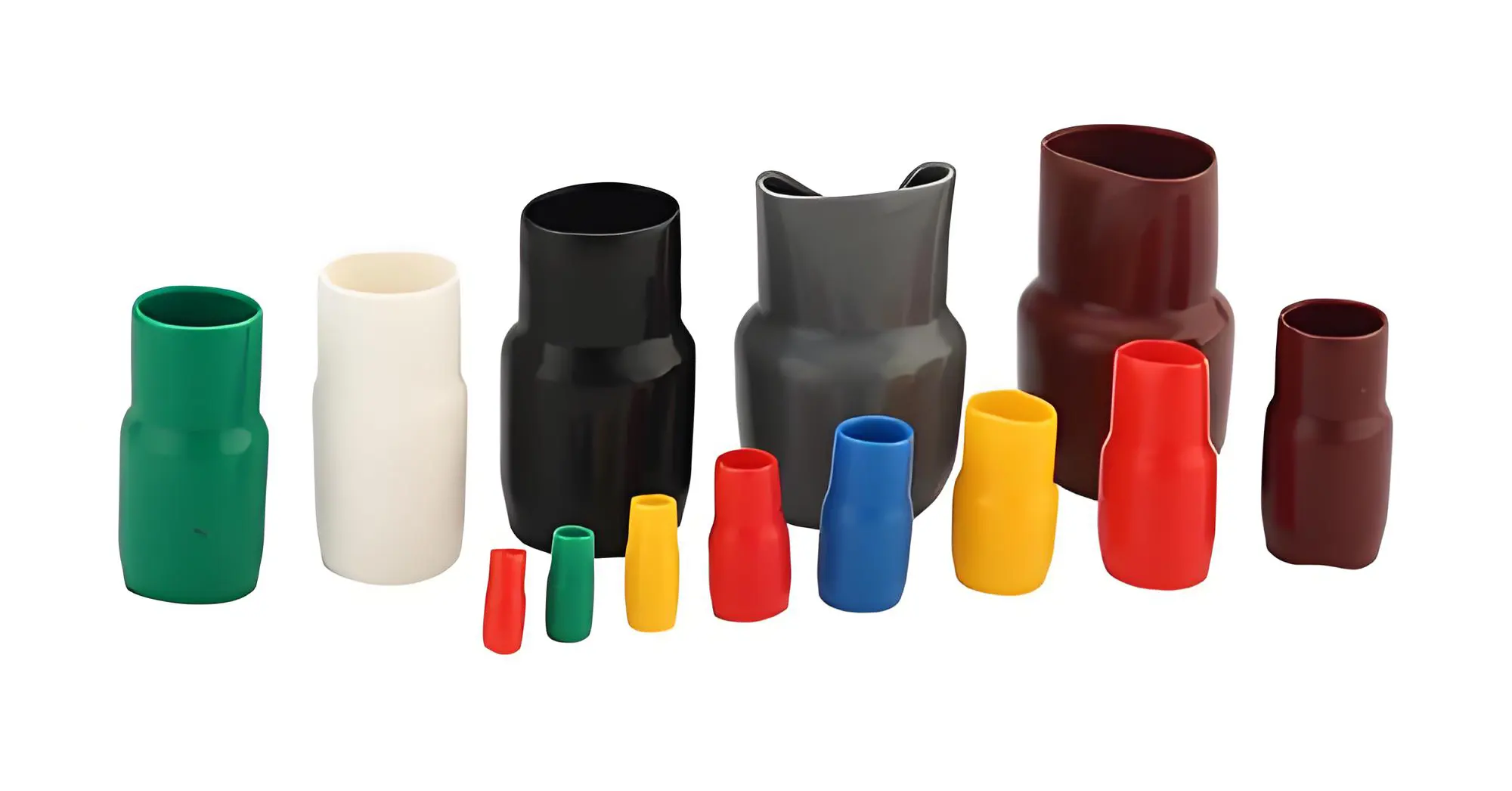
Core performance requirements
- Heat resistance: Passed 125 ℃ × 3000h thermal aging test (tensile strength retention rate ≥ 70%);
- Mechanical strength: Tensile strength ≥ 15MPa (TPU material can reach 35MPa);
- Flexibility: TPE/TPV material has a bending life of ≥ 500 times (without cracks);
- Flame retardancy: Complies with UL 94 V0 standard (vertical combustion self extinguishing time ≤ 30s);
- Environmental friendliness: Does not contain halogens and complies with the RoHS directive (TPU/PVC materials are preferred).
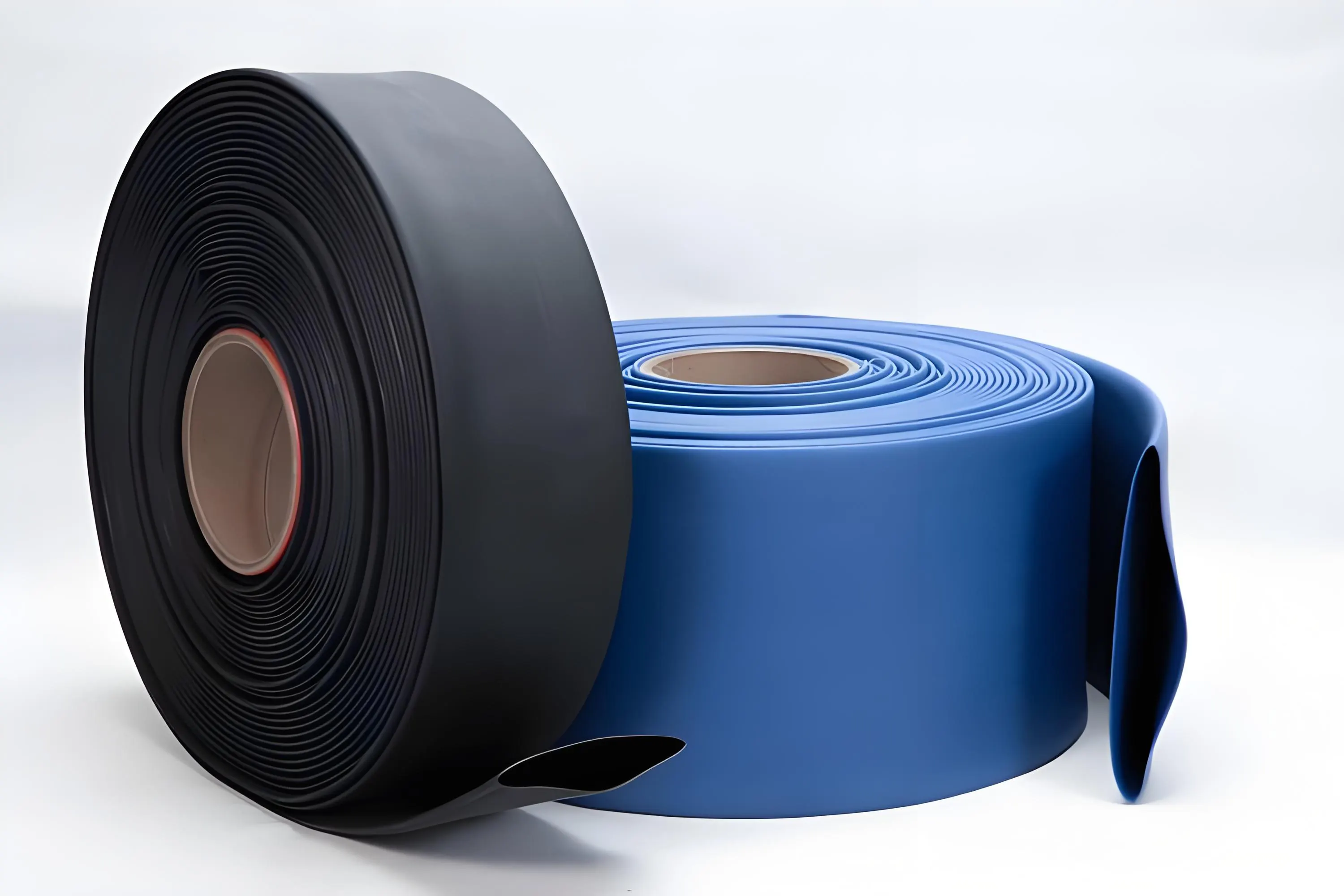
Material types and comparisons
Material type |
Typical representative |
Advantages and Characteristics |
Application scenarios |
TPE/TPV |
Thermoplastic elastomer/vulcanized rubber |
Chemical corrosion resistance, excellent flexibility (elongation ≥ 300%), suitable for frequent bending scenarios |
Industrial equipment motor harness, charging pile harness |
TPU |
Polyester thermoplastic polyurethane |
High wear resistance (Taber abrasion ≤ 40mg), tear strength ≥ 50N/mm, suitable for mechanical vibration environment |
Automotive chassis wiring harness, on-board charger output wiring harness |
Modified PVC |
Environmentally friendly and flame-retardant PVC sheath material |
Low cost (30% lower than TPU), easy to process, suitable for fixed wiring scenarios |
Photovoltaic cable protective layer |
silicone rubber |
Gas phase synthesis of silicone rubber (VMQ) |
Wide temperature resistance range (-60 ℃~200 ℃), UV aging resistance, but low mechanical strength (tensile strength ≥ 5MPa) |
High temperature sampling harness inside the battery |
Application scenarios
In the field of new energy vehicles
- Battery pack wiring harness: Silicone sheath resistant to electrolyte corrosion, suitable for high-voltage connections between battery modules;
- Drive motor harness: TPU material resistant to vibration fatigue, suitable for high temperature environments in motor cabins.
Industrial equipment
- High temperature sensor wiring harness: TPE sheath resistant to oil and acid alkali, used for metallurgical/chemical equipment ;
- Charging gun wiring harness: The modified PVC sheath has excellent flame retardancy and meets UL 758 electrical safety standard .
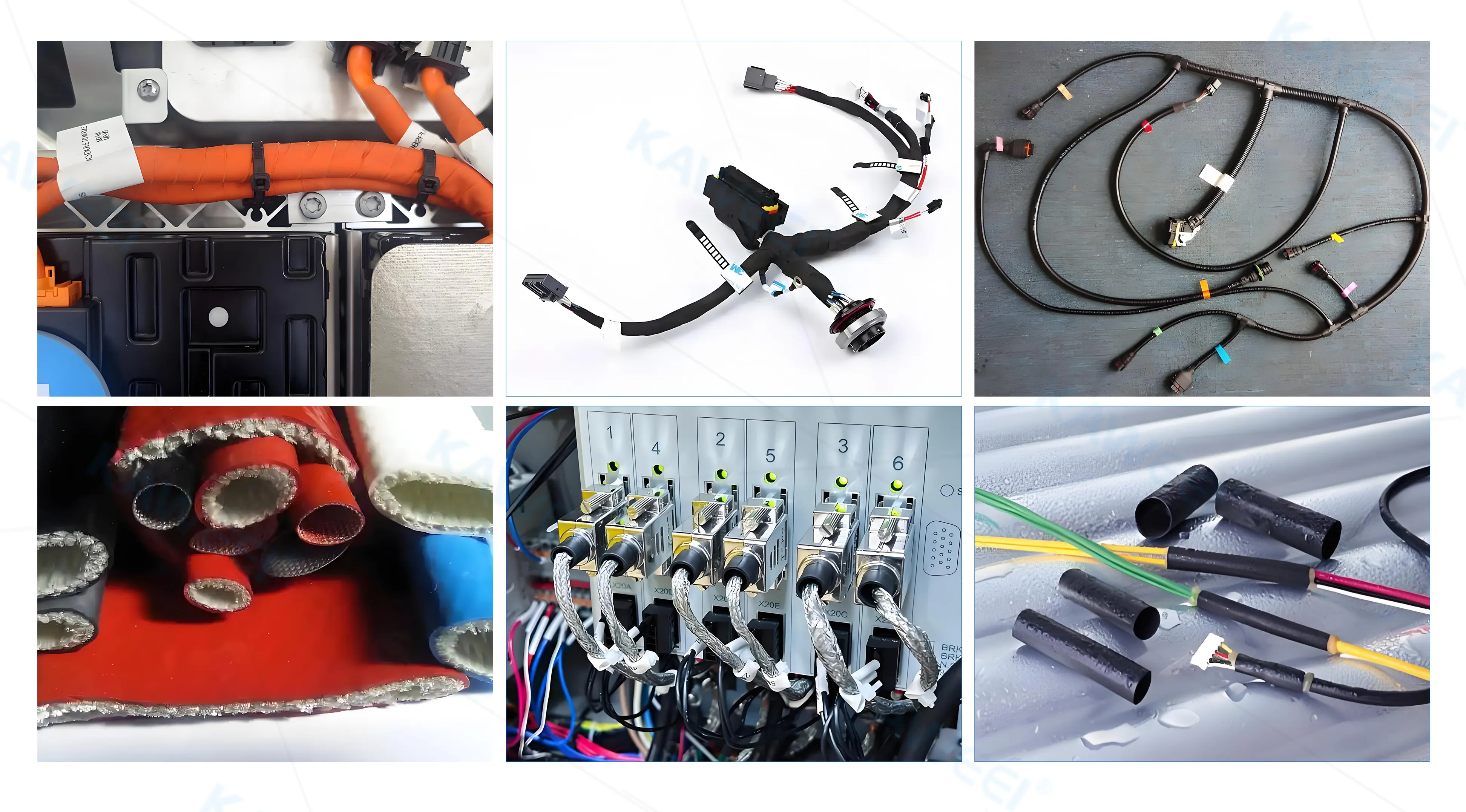
Architecture and Energy
- Photovoltaic cable sheath: environmentally friendly PVC material resistant to ultraviolet radiation, suitable for long-term outdoor laying;
- Energy storage system wiring harness: TPV sheath resistant to moisture and heat (humidity ≥ 95%), suitable for internal wiring of energy storage cabinets.
The necessity of 125 ℃ temperature resistant sheath material
High voltage system thermal load upgrade
- When the peak power of the motor exceeds 200kW, the surface temperature of the wire harness can reach 110 ℃ -125 ℃ (measured data);
- Under fast charging conditions, the charging harness generates Joule heat due to high current transmission, resulting in a local temperature rise exceeding 120 ℃.
Traditional material failure risk
- PVC material (with a temperature resistance of 105 ℃) undergoes accelerated aging at 125 ℃, resulting in cracking and decreased insulation performance;
- The failure to meet the standard for protective sheath materials increases the probability of wire harness short circuits by 3-5 times (industry statistics).