配線ハーネス製造工程の概要
- 2025-01-12 15:07:54
- 管理者より
配線ハーネスの製造プロセスフローは、主に以下の重要なステップをカバーします。第一に、ワイヤ、端子、コネクタ、ケーブルタイ、ワイヤ番号ラベル、絶縁テープ、熱収縮性スリーブなどを含む配線ハーネス材料の準備段階です。第二に、圧着機、熱収縮機、ハサミなどの製造工具や設備の準備作業を行う必要があります。様々な試験機器があらかじめ準備する必要があります。その後、実際の生産プロセスが開始され、設計要件に従ってワイヤの絶縁シースの一定の長さを剥離するワイヤ剥離作業が順次含まれます。その後、ワイヤ番号スリーブを行い、その後の組立とメンテナンス識別のために各ワイヤに対応する識別番号を正確に置きます。その後、端子クリップステップは、専門機器を通じて端子とワイヤをしっかりと接続するために行われます。次に、各コネクタが対応する端子とワイヤと正確にマッチすることを確認するためにコネクタアセンブリが行われます。組立が完了した後、配線ハーネスの全体的なレイアウトを整然と整理するために、配線と結合を行う必要があります。その後、配線ハーネスの厳格な試験が行われ、その電気性能と接続信頼性が基準を満たしているかどうかを確認します。最後に、それはワイヤハーネスの仕上げと倉庫の段階であり、適格なワイヤハーネスが適切に分類され、梱包され、指定されたエリアに保管されます。
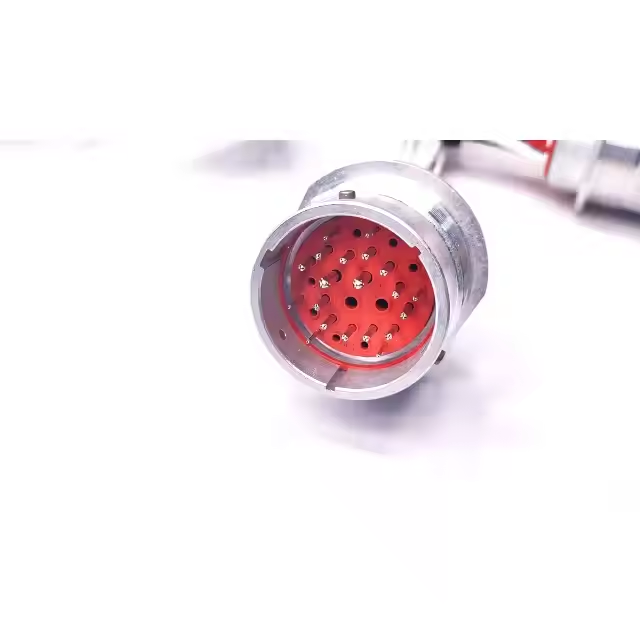
I 。主要なプロセス
(I)ターミナルクリミング
端子は、ワイヤと機器や機器を接続する重要なコンポーネントとして、ワイヤの電力と信号を伝送する責任があります。機器や機器への電力や信号の流入または流出は、すべて端末を通じて達成されています。したがって、ターミナルクリップの品質と関連する規格や仕様に準拠しているかどうかは、機器や機器の安定した正常な動作に直接影響します。ターミナルは主に 3 つのコア部分、すなわち、交尾領域、移行領域、およびクリンピング領域で構成されています。実際の生産プロセスでは、以下のクリンピング品質の問題が発生しやすいです。
- 異常な圧迫の高さ:クリップ高さは、特にクリップ操作が完了した後の導体クリップ領域の断面の高さを指し、クリップ品質を測定するための重要な指標です。クリミング高さが大きすぎると、ワイヤコアを効果的に圧縮できず、クリミング領域に比較的大きな無効なボイドが生じます。ワイヤと端子金属の有効接触面積が大幅に減少するため、接触抵抗が大幅に増加し、加熱現象を引き起こし、重症では端子を燃焼させることさえあります。逆に、クリップ高さが小さすぎると、ケーブルの引力と定格電流承受能力が大幅に低下し、ワイヤコアが粉砕されたり、端子のクリップ領域が壊れたり、ワイヤ接続が壊れ、最終的に開回路障害が発生する可能性があります。ターミナルクリップの品質を確保するためには、マイクロメーターなどのプロの測定ツールを使用してクリップ後の製品を正確に測定し、クリップピンチとクリップ機器を定期的に校正する必要があります。
- 絶縁体クリッピング領域のサイズにおける偏差: ワイヤの種類、仕様、端末の種類が多様であるため、現在、統一された定量規制はなく、オペレータは実際の操作で蓄積した経験に頼って制御しています。絶縁体クリップの主な機能は、導体クリップ領域の応力緩和を提供し、ケーブルが曲げられたときに、絶縁体クリップ領域の緩衝効果でワイヤクリップ領域の破損を避けることができます。したがって、高品質の絶縁層クランプは、ワイヤクランプ効果を保護するために非常に重要です。絶縁層クリップが小さすぎると、絶縁層クリップ領域の金属応力が急激に増加し、応力緩和機能が著しく弱まります。逆に、絶縁層クリップが大きすぎると、ワイヤクリップ領域に対する応力緩衝効果が大幅に低下します。実際の運用では、通常、目視観察と手でワイヤを優しく揺さぶることによって判断され、絶縁圧迫領域が揺れないという基準があります。
- 緩い導体圧着領域の問題: これは、ターミナルクリッププロセスで最も一般的な品質問題の 1 つであり、クリップ失敗の主な原因でもあります。すべてのワイヤコアが導体クランプ領域に完全に閉じ込められていない状況が発生すると、クランプされた部品の強度と電流負荷容量が大幅に低下します。この問題に対する解決策は比較的簡単です。ケーブルをバンドルに再バンドルし、圧縮されるターミナルに挿入してください。ケーブルからの絶縁層の剥離は独立した操作プロセスであることに注意してください。このプロセスでは、不適切な取り扱いやバンドルにより、誤ってワイヤコアを分離することが非常に容易です。したがって、ワイヤ剥離作業には特殊なワイヤ剥離ピンチを使用し、ケーブル上の端子とクリムする準備ができるまで絶縁スリーブがケーブルから完全に落ちないように、取り外される絶縁層の長さを正確に制御することをお勧めします。このようにして、ワイヤコア緩み問題の発生確率が最小限に抑えられます。
- 不適切なワイヤの剥ぎ取りの長さ: ワイヤ剥離作業中は、ワイヤ剥離長さがちょうど正しいことを確認する必要があります。ワイヤ剥離が短すぎると、端子クリップ段階では、ワイヤが導体クリップ領域に完全に挿入できず、端子とワイヤ間のクリップ力が引張試験の要件を満たすことができません。振動の影響を受けた機関車の運転中に、ワイヤが落ちる可能性が非常に高い。同時に、ワイヤと端子間の接触金属面が減少しているため、ここでは激しい加熱が発生し、開回路故障さえ発生する可能性があります。この問題に対処するには、ワイヤ剥離長さを厳密に制御して十分な余裕を確保し、ワイヤをクリミング中にクリミング領域に完全に挿入する必要があります。
- 過剰なワイヤー挿入深さ: 短すぎるワイヤストリッピングの問題とは対照的に、ワイヤが挿入されすぎたり、遷移領域にも入っていれば、ワイヤコアが長すぎるとピンが正しく挿入されず、 2 つのコネクタのワイヤ間の接触が悪くなり、最終的には信号中断につながる可能性があります。また、ワイヤの挿入が過剰なため、 2 つの回路間に短絡が発生するという共通な欠陥があります。例えば、機関車の牽引モータ速度センサのコネクタでは、この状況により複数の機関車の故障を引き起こしています。このような品質問題を解消するためには、長すぎないようにワイヤ剥離長さを厳格に制御するとともに、ワイヤを圧着する際の適切なワイヤ挿入量を正確に制御する必要があります。
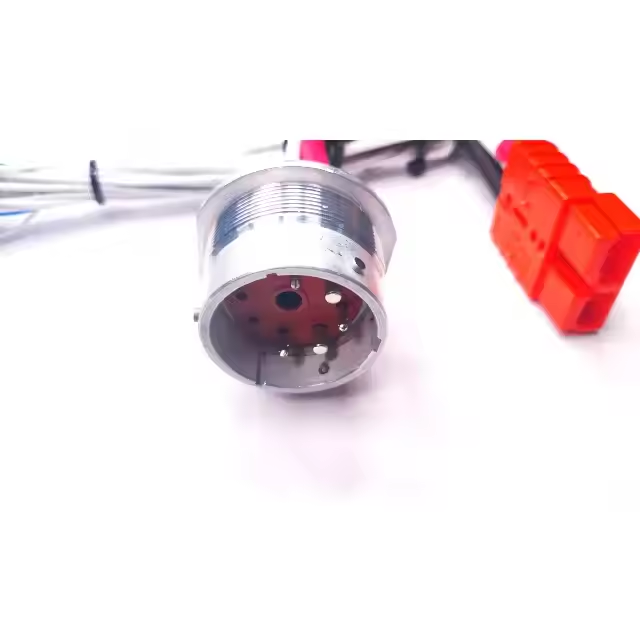
(II)コネクタアセンブリ
コネクタ組立プロセスでは、以下の重要なポイントを強調する必要があります。
- 機関車に使用されるコネクタの種類は数多く複雑です。多くのコネクタは外観が非常に似ているが内部構造が異なる。したがって、組立作業中は、オペレータは材料ラックコードに従って材料を正確にピックする必要があります。材料を取得した後、材料の正しい選択を確実にするために、操作説明書と詳細な比較を行う必要があります。
- 端子をコネクタソケットに挿入する際には、適切な力を習得する必要があります。鮮明な「クリック」音が聞こえると、端子が挿入されたことを示し、この時点では引き続き力を加えることはできません。実際の生産現場では、オペレータが外観だけで挿入状況を判断するため、多くの品質問題が生じています。
- 組み立てられたコネクタは適切に保護する必要があります。ほとんどのコネクタは機関車信号線や制御線に適用されているため、生産現場のほこりや湿気がコネクタの内部に容易に浸透し、隣接する線間の短絡が発生し、信号の正常な伝達を深刻に妨害し、機関車や車両の制御にさらに影響を与える可能性があります。この目的のために、コネクタに付属する保護カバーを使用して、コネクタ全体をしっかりと覆って締め付け、アセンブリ品質を確保する必要があります。