Le flux de processus de fabrication du faisceau de câblage couvre principalement les étapes clés suivantes : Tout d'abord, il s'agit de l'étape de préparation des matériaux de câblage, qui comprennent les fils, les bornes, les connecteurs, les liaisons de câble, les étiquettes de numéro de fil, les bandes isolantes, les manchons thermiquement rétractables, etc. Deuxièmement, le travail de préparation des outils et équipements de fabrication devrait être fait, tels que les machines à crimpage, les machines à rétrécissement thermique, les ciseaux, et divers équipements d'essai, qui doivent tous être préparés à l'avance. Par la suite, le processus de production réel commence, qui comprend successivement l'opération de décapage du fil, c'est - à - dire le décapage d'une certaine longueur de la gaine isolante du fil selon les exigences de conception ; puis, le manchon de numéro de fil est effectué pour mettre avec précision les numéros d'identification correspondants sur chaque fil pour l'identification ultérieure de l'assemblage et de l'entretien ; après cela, l'étape de crimpage des bornes est effectuée pour relier étroitement les bornes et les fils à travers l'équipement professionnel ; Ensuite, l'assemblage du connecteur est effectué pour s'assurer que chaque connecteur s'accouple avec précision avec les bornes et les fils correspondants ; après l'assemblage est terminé, le câblage et la liaison doivent être effectués pour rendre la disposition globale du faisceau de câblage soignée et organisée ; puis, un essai strict du faisceau de câblage est effectué pour vérifier si ses performances électriques et sa fiabilité de connexion répondent aux normes ; Enfin, il s'agit de l'étape de finition et d'entreposage du câblage, où les câblages qualifiés sont correctement triés, emballés et stockés dans la zone désignée.
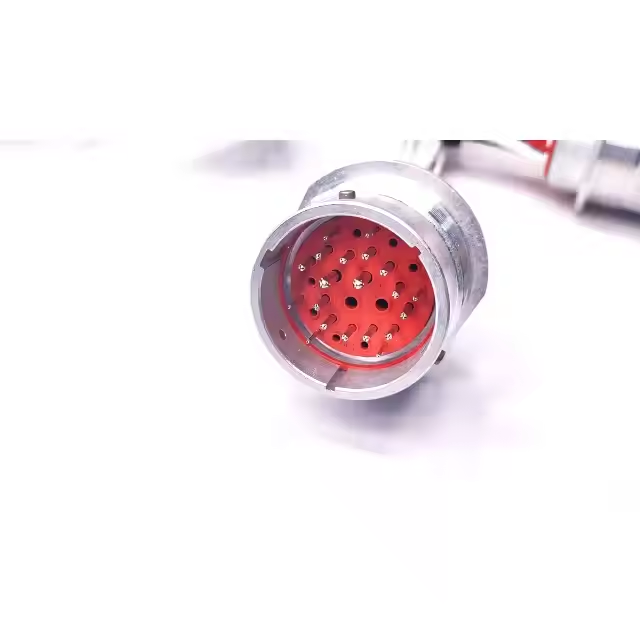
I. Processus clés
(I)Crimpage terminal
Les terminaux, en tant que composants cruciaux reliant les fils et les instruments ou équipements, sont chargés de transmettre la puissance et les signaux des fils. L'entrée ou la sortie de puissance et de signaux vers ou depuis les instruments ou l'équipement sont tous obtenus par des terminaux. Par conséquent, la qualité du crimpage terminal et sa conformité avec les normes et spécifications pertinentes affectent directement le fonctionnement stable et normal des instruments ou des équipements. Un terminal se compose principalement de trois parties centrales, à savoir la zone d'accouplement, la zone de transition et la zone de crimpage. Dans le processus de production réel, les problèmes de qualité de crimpage suivants sont susceptibles de se produire :
- Hauteur de crimpage anormale :La hauteur de serrage se réfère spécifiquement à la hauteur de la section transversale de la zone de serrage du conducteur après l'opération de serrage est terminée, et c'est un indicateur clé pour mesurer la qualité du serrage. Si la hauteur de crimpage est trop grande, les noyaux de fil ne peuvent pas être efficacement comprimés, ce qui entraîne un vide inefficace relativement grand dans la zone de crimpage.Étant donné que la surface de contact effective entre le fil et le métal terminal est considérablement réduite, la résistance au contact augmentera considérablement, provoquant des phénomènes de chauffage et, dans les cas graves, même brûler les bornes. Inversement, si la hauteur de serrage est trop petite, la force de traction et la capacité de charge du courant nominal du câble seront considérablement réduites, ce qui peut entraîner l'écrasement des noyaux de fil ou la rupture de la zone de serrage de la borne, provoquant la rupture de la connexion de fil et finalement une défaillance de circuit ouvert. Pour assurer la qualité du crimpage terminal, des outils de mesure professionnels tels que les micromètres doivent être utilisés pour mesurer avec précision les produits après le crimpage, et les pinces de crimpage et l'équipement de crimpage doivent être calibrés régulièrement.
- Déviation de la taille de la zone de crimpage d'isolation : Compte tenu de la grande variété de types de fils, de spécifications et de types de bornes, il n'existe actuellement pas de réglementation quantitative unifiée et les opérateurs s'appuient principalement sur l'expérience accumulée dans les opérations réelles pour contrôler. La fonction principale du crimpage d'isolation est de fournir un soulagement de contrainte pour la zone de crimpage du conducteur, en veillant à ce que lorsque le câble est plié, la zone de crimpage du fil puisse éviter d'être cassée avec l'effet tampon de la zone de crimpage d'isolation. Par conséquent, le crimpage de la couche isolante de haute qualité est d'une grande importance pour protéger l'effet de crimpage du fil. Si le crimpage de la couche d'isolation est trop petit, la contrainte métallique dans la zone de crimpage de l'isolation augmentera fortement et la fonction de soulagement de contrainte sera sévèrement affaiblie ; inversement, si le crimpage de la couche d'isolation est trop grand, son effet tampon de contrainte sur la zone de crimpage du fil sera considérablement réduit. En fonctionnement réel, il est généralement jugé par observation visuelle et secouant doucement le fil à la main, avec le critère que la zone de crimpage de l'isolation ne tremble pas.
- Problème de zone de crimpage du conducteur lâche : C'est l'un des problèmes de qualité les plus courants dans le processus de crimpage du terminal et c'est également la principale cause de défaillance du crimpage. Une fois que la situation se produit où tous les noyaux de fil ne sont pas complètement enfermés dans la zone de crimpage du conducteur, la résistance et la capacité de charge actuelle des pièces crimpées seront considérablement réduites. La solution de ce problème est relativement simple. Il suffit de regrouper les câbles en un faisceau, puis de les insérer dans le terminal pour être crimpé. Il convient de noter que le décapage de la couche isolante du câble est un processus d'opération indépendant. Au cours de ce processus, en raison d'une manipulation ou d'un regroupement incorrect, il est très facile de séparer accidentellement les noyaux de fil. Par conséquent, il est recommandé d'utiliser des pinces de décapage de fil spéciales pour les opérations de décapage de fil et de contrôler avec précision la longueur de la couche isolante retirée pour s'assurer que le manchon isolant ne tombe pas complètement du câble jusqu'à ce qu 'il soit prêt à être serré avec la borne sur le câble. De cette façon, la probabilité d'occurrence du problème de relâchement du noyau de fil peut être minimisée.
- Longueur de fil de décapage incorrecte : Pendant l'opération de décapage du fil, il est nécessaire de s'assurer que la longueur de décapage du fil est juste la bonne. Si le décapage du fil est trop court, au stade de crimpage du terminal, le fil ne peut pas être complètement inséré dans la zone de crimpage du conducteur et la force de crimpage entre le terminal et le fil ne peut pas répondre aux exigences de l'essai de traction. Pendant le fonctionnement de la locomotive, affectée par les vibrations, le fil est très susceptible de tomber. Dans le même temps, étant donné que la surface métallique de contact entre le fil et la borne est réduite, un chauffage sévère se produira ici et même une défaillance de circuit ouvert peut être causée. Pour résoudre ce problème, la longueur de décapage du fil doit être strictement contrôlée pour assurer une marge suffisante, et le fil doit être complètement inséré dans la zone de crimpage pendant le crimpage.
- Profondeur d'insertion de fil : Contrairement au problème du décapage de fil trop court, si le fil est inséré trop et entre même dans la zone de transition, le noyau de fil trop long peut empêcher la broche d'être insérée correctement, ce qui entraîne un mauvais contact entre les fils des deux connecteurs et conduit finalement à une interruption du signal. En outre, il y a une défaut commune, c'est - à - dire qu 'en raison d'une insertion excessive de fil, un court-circuit se produit entre deux circuits. Par exemple, dans le connecteur du capteur de vitesse du moteur de traction de la locomotive, plusieurs défaillances de locomotive ont été causées en raison de cette situation. Pour éliminer ces problèmes de qualité, il est nécessaire de contrôler strictement la longueur de décapage du fil pour éviter d'être trop longue et, en même temps, de contrôler avec précision la quantité appropriée d'insertion de fil lors du sertissage du fil.
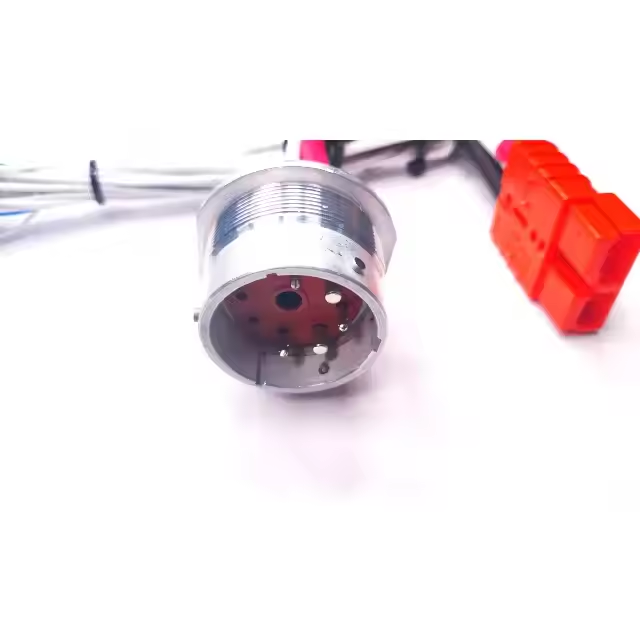
(II)Connecteur Assembly
Les points clés suivants doivent être soulignés dans le processus d'assemblage du connecteur :
- Les types de connecteurs utilisés dans les locomotives sont nombreux et complexes. Beaucoup de connecteurs ont une apparence très similaire mais des structures internes complètement différentes. Par conséquent, lors de l'opération d'assemblage, les opérateurs doivent choisir avec précision les matériaux selon le codage du rack de matériaux. Après avoir obtenu les matériaux, ils doivent faire une comparaison détaillée avec le livre d'instructions d'utilisation pour assurer la sélection correcte des matériaux.
- Lors de l'insertion de la borne dans la prise du connecteur, une force appropriée doit être maîtrisée. Lorsqu ' un bruit de « clic » net est entendu, cela indique que le terminal a été inséré en place et, à ce moment-là, il n'est pas autorisé à continuer à appliquer la force. Dans le site de production réel, de nombreux problèmes de qualité ont été causés parce que les opérateurs jugent la situation d'insertion uniquement par l'apparence.
- Les connecteurs assemblés doivent être protégés correctement.Étant donné que la plupart des connecteurs sont appliqués aux lignes de signal de locomotive et aux lignes de commande, la poussière et l'humidité sur le site de production peuvent facilement pénétrer à l'intérieur des connecteurs, entraînant des courts-circuits entre les lignes adjacentes, interférant sérieusement avec la transmission normale des signaux et affectant davantage le contrôle des locomotives et des véhicules.À cette fin, le couvercle de protection fourni avec le connecteur doit être utilisé pour recouvrir et fixer étroitement l'ensemble du connecteur afin d'assurer la qualité de l'assemblage.