Der Fertigungsprozess des Drahtgürts umfasst hauptsächlich die folgenden Schlüsselschritte: Erstens ist es die Vorbereitungsphase von Drahtgärtenmaterialien, zu denen Drähte, Klemmungen, Steckverbinder, Kabelbindungen, Drahtnummeretiketten, Isolierbänder, wärmezschrumpfbare Hülsen usw. gehören Zweitens sollte die Vorbereitungsarbeit von Fertigungswerkzeugen und Ausrüstungen durchgeführt werden, wie Crimpfmaschinen, wärmezschrumpfmaschinen, Schere, und verschiedene Prüfgeräte, die alle im Voraus vorbereitet werden müssen. Anschließend beginnt der eigentliche Produktionsprozess, der nacheinander den Drahtstripper Betrieb umfasst, d. h. das Entziehen einer bestimmten Länge der Isolierhülle des Drahtes gemäß den Entwurfsanforderungen; dann wird die Drahtnummer-Hülse durchgeführt, um die entsprechenden Identifikationsnummern auf jeden Draht für die anschließende Montage - und Wartungsidentifikation genau zu legen; Danach wird der Terminalschritt durchgeführt, um die Klemmen und Drähte durch professionelle Ausrüstung fest zu verbinden; Als nächstes wird die Steckverbindermontage durchgeführt, um sicherzustellen, dass jeder Steckverbinder genau mit den entsprechenden Klemmen und Drähten passt; nach der Montage abgeschlossen ist, müssen Verkabelung und Bindung durchgeführt werden, um das Gesamtlayout des Drahtgurts sauber und organisiert zu machen; dann wird strenge Prüfung des Drahtgurts durchgeführt, um zu überprüfen, ob seine elektrische Leistung und Verbindungszuverlässigkeit den Standards entsprechen; Schließlich ist es die Bearbeitung und Lagerung der Drahtgurte, in der die qualifizierten Drahtgurte ordnungsgemäß sortiert, verpackt und in dem vorgesehenen Bereich gelagert werden.
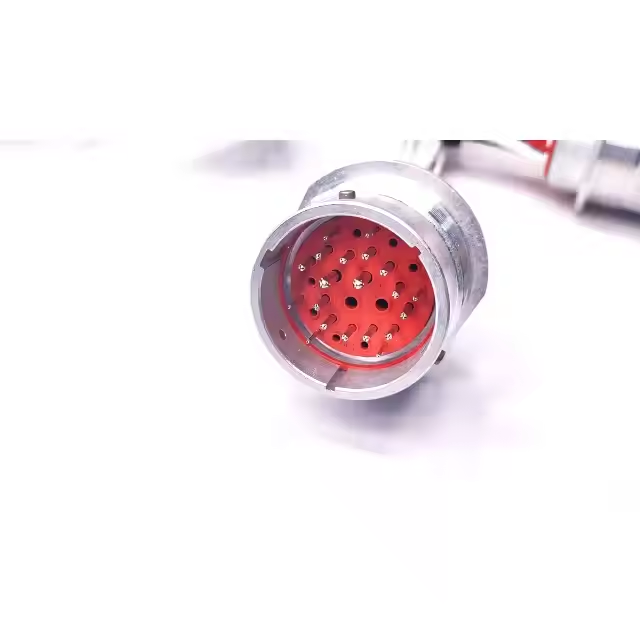
I. Schlüsselprozesse
(I)Terminal Crimping
Terminals, als entscheidende Komponenten, die Drähte und Instrumente oder Geräte verbinden, tragen die Verantwortung für die Übertragung der Leistung und Signale der Drähte. Der Ein - oder Abfluss von Energie und Signalen zu oder von den Instrumenten oder Geräten erfolgt über Terminals. Daher beeinflusst die Qualität des Terminalscrimens und ob es den relevanten Normen und Spezifikationen entspricht, direkt den stabilen und normalen Betrieb der Instrumente oder Ausrüstung. Ein Terminal besteht hauptsächlich aus drei Kernteilen, nämlich dem Paarungsbereich, dem Übergangsbereich und dem Crimpfbereich. Im tatsächlichen Produktionsprozess sind die folgenden Crimp-Qualitätsprobleme wahrscheinlich auftreten:
- Abnormale Crimping-Höhe:Die Crimphöhe bezieht sich insbesondere auf die Höhe des Querschnitts des Leitercrimpfbereichs nach Abschluss des Crimpvorgangs und ist ein wichtiger Indikator für die Messung der Crimpqualität. Wenn die Crimphöhe zu groß ist, können die Drahtkerne nicht effektiv komprimiert werden, was zu einer relativ großen ineffektiven Leere im Crimpfbereich führt. Da die effektive Kontaktfläche zwischen dem Draht und dem Terminalsmetall stark reduziert wird, wird der Kontaktwiderstand signifikant erhöht, was zu Erwärmungsphänomenen und in schweren Fällen sogar zu Verbrennungen der Terminals führt. Umgekehrt, wenn die Krimpfhöhe zu klein ist, wird die Zugkraft und die Nennstromkapazität des Kabels stark reduziert, was dazu führen kann, dass die Drahtkerne zerkleinert werden oder der Krimpfbereich des Terminals gebrochen wird, wodurch die Drahtverbindung brechen und letztendlich zu einem offenen Schaltkreisfehler führt. Um die Qualität des Terminalscrimpings zu gewährleisten, sollten professionelle Messwerkzeuge wie Mikrometer verwendet werden, um die Produkte nach dem Crimping genau zu messen, und die Crimpingzangen und Crimping-Ausrüstung sollten regelmäßig kalibriert werden.
- Abweichung in der Größe des Crimping-Bereiches der Isolation: Angesichts der Vielzahl von Drahtarten, Spezifikationen und Terminals gibt es derzeit keine einheitliche quantitative Regulierung, und die Betreiber verlassen sich hauptsächlich auf die Erfahrung, die im tatsächlichen Betrieb gesammelt wurde, um zu kontrollieren. Die Hauptfunktion des Isolierkrimpfs besteht darin, Spannungsentlastung für den Leiterkrimpfbereich zu gewährleisten, sodass, wenn das Kabel gebogen ist, der Drahtkrimpfbereich mit dem Puffereffekt des Isolierkrimpfbereichs verhindert werden kann. Daher ist das Crimping von hochwertiger Isolierschicht von großer Bedeutung für den Schutz des Drahtkrimpfeffekts. Wenn das Crimping der Isolierschicht zu klein ist, wird die Metallspannung im Crimping-Bereich der Isolierung stark zunehmen und die Spannungsentlastungsfunktion wird stark geschwächt; umgekehrt, wenn das Crimping der Isolierschicht zu groß ist, wird der Spannungspuffer-Effekt auf den Drähtecrimping-Bereich stark reduziert. Im tatsächlichen Betrieb wird es normalerweise durch visuelle Beobachtung und sanftes Schütteln des Drahtes von Hand beurteilt, mit dem Kriterium, dass der Isolierkrimpfbereich nicht zittert.
- Loose Conductor Crimping Area Problem: Dies ist eines der häufigsten Qualitätsprobleme im Terminalcrimping-Prozess und ist auch die Hauptursache für Crimping-Fehler. Sobald die Situation auftritt, in der alle Drahtkerne nicht vollständig im Leiterkrimpfbereich eingeschlossen sind, wird die Festigkeit und die Stromlastkapazität der gekrimpften Teile stark reduziert. Die Lösung dieses Problems ist relativ einfach. Bündeln Sie einfach die Kabel erneut in ein Bündel und legen Sie sie dann in das Terminal ein, um gekrümmt zu werden. Es sollte beachtet werden, dass das Entfernen der Isolierschicht vom Kabel ein unabhängiger Betriebsprozess ist. Während dieses Prozesses ist es aufgrund unsachgemäßer Handhabung oder Bündelung sehr leicht, die Drahtkernen versehentlich zu trennen. Daher wird empfohlen, spezielle Drahtentstreifungszangen für Drahtentstreifungsvorgänge zu verwenden und die Länge der entfernten Isolierschicht genau zu steuern, um sicherzustellen, dass die Isolierhülse nicht vollständig vom Kabel fällt, bis sie bereit ist, mit dem Anschluss am Kabel gekrümmt zu werden. Auf diese Weise kann die Auftretenwahrscheinlichkeit des Drahtkern-Lock - Problems minimiert werden.
- Ungemessene Drahtstreifenlänge: Während des Drahtstreifenvorgangs muss sichergestellt werden, dass die Drahtstreifenlänge genau richtig ist. Wenn das Drahtstreifen zu kurz ist, kann der Draht nicht vollständig in den Krimpfbereich des Leiters eingegeben werden, und die Krimpfkraft zwischen dem Terminal und dem Draht kann die Anforderungen des Zugtests nicht erfüllen. Während des Betriebs der Lokomotive, die von Vibrationen betroffen ist, ist es sehr wahrscheinlich, dass der Draht abfällt. Zur gleichen Zeit, da die Kontaktmetalloberfläche zwischen dem Draht und dem Klemm reduziert wird, tritt hier eine starke Erwärmung auf und kann sogar ein offener Schaltkreisfehler verursacht werden. Um dieses Problem zu lösen, sollte die Drahtstreifenlänge streng kontrolliert werden, um ausreichende Spielräume zu gewährleisten, und der Draht sollte während des Crimpings vollständig in den Crimpfbereich eingefügt werden.
- Übermäßige Drahttiefe: Im Gegensatz zu dem Problem des zu kurzen Drahtstripens kann der zu lange Drahtkern, wenn der Draht zu viel eingefügt wird und sogar in den Übergangsbereich eintritt, verhindern, dass der Pin korrekt eingefügt wird, was zu einem schlechten Kontakt zwischen den Drähten der beiden Steckverbinder führt und letztendlich zu Signalunterbrechung führt. Darüber hinaus gibt es einen gemeinsamen Fehler, d. h. durch übermäßiges Draht-Einfügen, tritt ein Kurzschluss zwischen zwei Schaltkreisen auf. Beispielsweise wurden im Steckverbinder des Traktionsmotorgeschwindigkeitssensors von Lokomotiven aufgrund dieser Situation mehrere Lokomotivenausfälle verursacht. Um solche Qualitätsprobleme zu beseitigen, ist es notwendig, die Drahtstreifenlänge strikt zu kontrollieren, um zu lang zu sein und gleichzeitig die angemessene Menge an Draht-Einfügung beim Krimpfen des Drahtes genau zu kontrollieren.
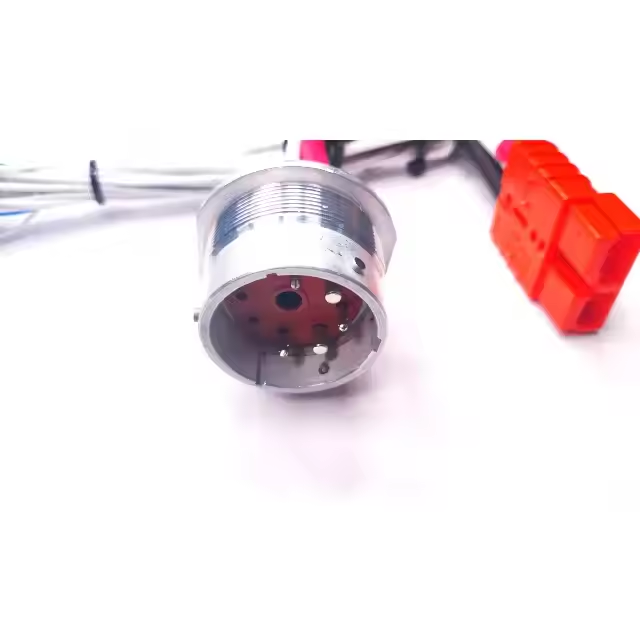
(II)Connector Assembly
Die folgenden Schlüsselpunkte müssen im Steckverbindermontageprozess betont werden:
- Die Arten von Steckverbindern, die in Lokomotiven verwendet werden, sind zahlreich und komplex. Viele Steckverbinder haben sehr ähnliches Erscheinungsbild, aber völlig unterschiedliche interne Strukturen. Daher müssen die Bediener während des Montagevorgangs Materialien gemäß der Materialregal-Codierung genau auswählen. Nachdem sie die Materialien erhalten haben, müssen sie einen detaillierten Vergleich mit dem Betriebsanleitungbuch vornehmen, um die richtige Auswahl der Materialien sicherzustellen.
- Beim Einfügen des Klemmers in die Steckverbinderbuchse muss eine angemessene Kraftmenge beherrscht werden. Wenn ein klares "Klick" - Geräusch zu hören ist, zeigt es an, dass das Terminal an Ort und Stelle eingeführt wurde, und zu diesem Zeitpunkt ist es nicht erlaubt, weiter Kraft auszuüben. Im eigentlichen Produktionsstandort sind viele Qualitätsprobleme verursacht worden, da die Bediener die Einfügungssituation nur anhand des Erscheinens beurteilen.
- Die zusammengebauten Steckverbinder müssen ordnungsgemäß geschützt werden. Da die meisten Steckverbinder auf Lokomotivsignalleitungen und Steuerleitungen angewendet werden, können Staub und Feuchtigkeit in der Produktionsstätte leicht in das Innere der Steckverbinder eindringen, was zu Kurzschlüssen zwischen benachbarten Leitungen führt, was die normale Signalübertragung ernsthaft stört und die Steuerung von Lokomotiven und Fahrzeugen weiter beeinträchtigt. Zu diesem Zweck sollte die mit dem Steckverbinder ausgestattete Schutzabdeckung verwendet werden, um den gesamten Steckverbinder fest abzudecken und zu befestigen, um die Montagequalität zu gewährleisten.